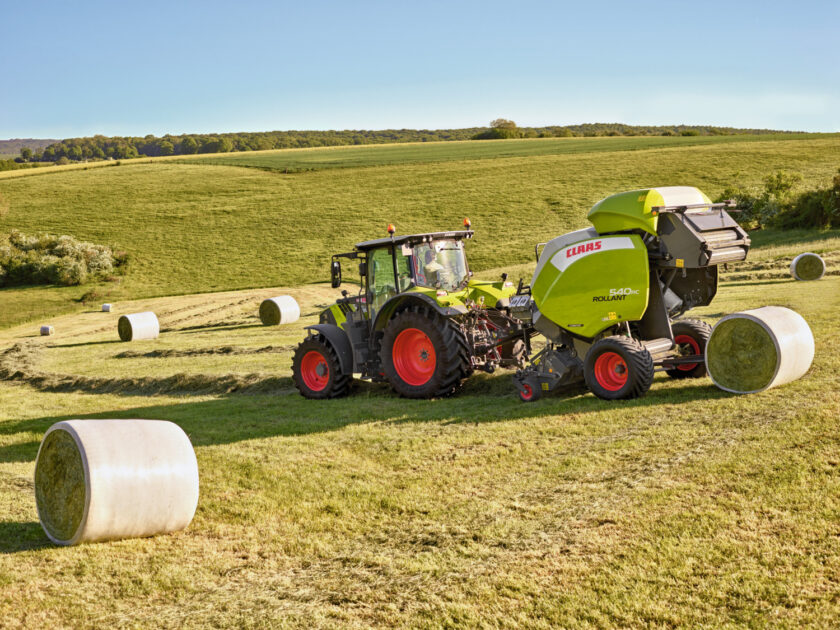
A continuous thread unites the evolution of the Claas brand from its origins to the present day: quality. This hallmark has been represented since the early decades of the 20th century by the balers designed and developed by the company in Harsewinkel. This quality stems particularly from an innovative tying system patented in 1921 by August Claas, the company’s founder, and remains the cornerstone of the German Group’s forage harvester range over a century later. Both the variable chamber “Variant” balers and the fixed chamber “Rollant” models share a primary feature: the ability to combine maximum press density with a tying system that securely wraps the produced bale.
This ensures optimal transportation and storage processes for the finished product, reducing unused space and operational costs related to moving between the field and the company site. These advantages are further highlighted in the “Variant 500” series, which allows all operational functions to be electronically programmed and monitored in real-time via the seven-inch isobus “Cebis 700” terminal from the tractor cab. This terminal enables the setting of the dimensional and pressing characteristics of each bale. The four models in the “Variant 500” series, named “560 Rf/Rc,” “580 Rf/Rc,” “565 Rc Pro,” and “585 Rc Pro,” the latter in “Hd” version, can produce finished products with diameters ranging from a minimum of 90 to a maximum of 180 centimeters and a fixed width of 120 centimeters.
Claas round balers: no problem on uneven terrain
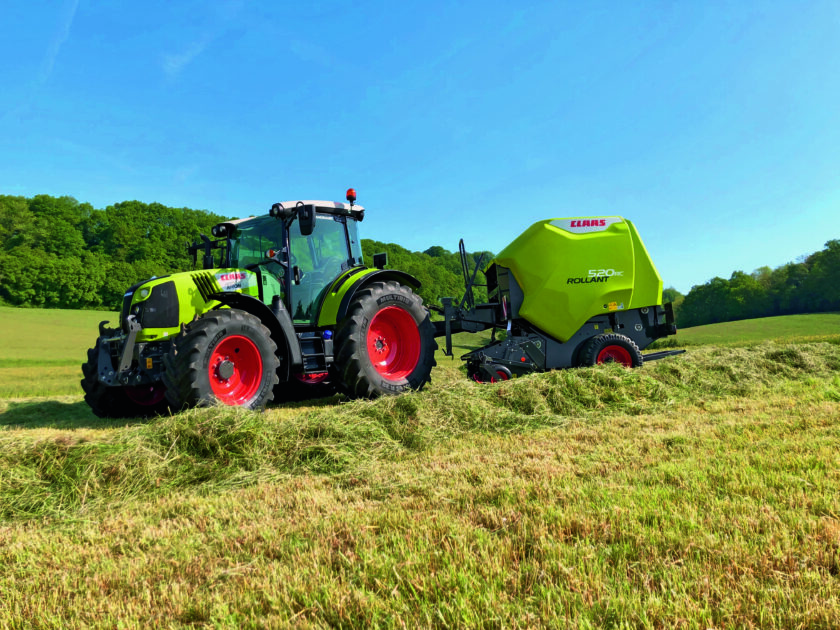
These parameters are managed by electronic control units that specifically regulate the hydraulic cylinders controlling the tension of the belts for final bale processing. This system works in conjunction with pick-ups characterized by two different widths, 210 and 235 centimeters, creating working fronts of 190 and 215 centimeters respectively. Regardless of this parameter, their terrain contouring remains optimal due to height-adjustable, oscillating gauge wheels that allow the balers to closely follow even the smallest elevation changes. The steel teeth on the pick-ups protect the unit from impacts with stones or other foreign objects. Once fieldwork is completed, the pick-up wheels can be lifted off the ground via an optional tilting mechanism, simplifying and speeding up road transport. Additionally, the “Variant 500” can be optionally equipped with a double roller pre-compactor to accelerate the flow of collected material to the “Roto Feed” or “Roto Cut” rotors. The “Roto Feed” is devoid of cutting elements, while the “Roto Cut” operates 360 degrees with star-shaped teeth of six millimeters thickness paired with cutting units equipped with 14 knives.
Up to 17 Knives with the “Hd” Versions
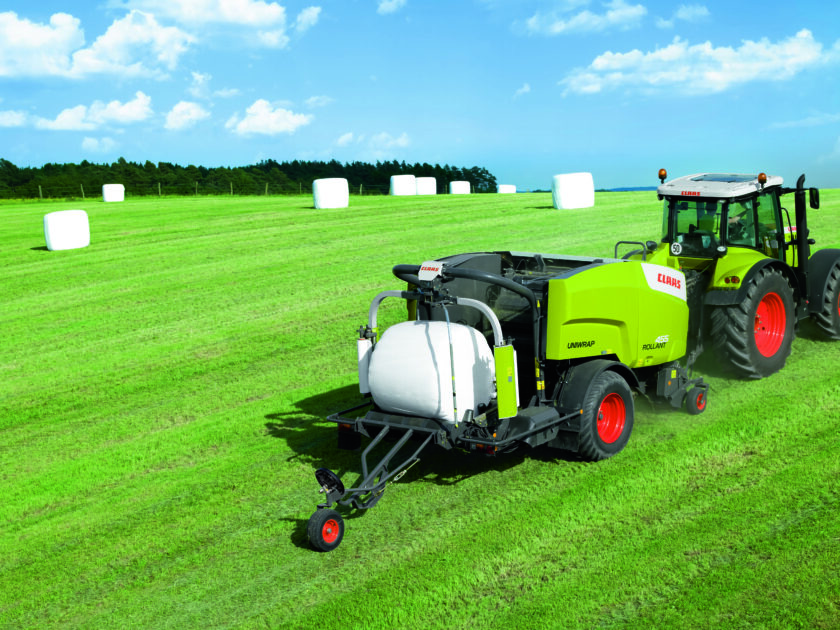
The star-shaped teeth on the “Hd” (Heavy Duty) versions are thicker at eight millimeters and work with 17 knives to produce shorter lengths of around 60 millimeters compared to the approximately 70 millimeters produced by the 14-knife system. The “Hd” versions also feature the standard “Pro” anti-clogging system, which is openable and equipped with an integrated pre-alarm system, facilitating material conveyance to the pressing chamber. Inside the chamber, a double tensioning arm benefits from a pressure regulation system that separates the action of the two tensioning units.
Operators can monitor the position and pressure of each arm precisely. The “Smart Density” system optimizes the entire process by continuously adjusting the machine’s power requirements based on programmed inputs, creating softer or harder bale cores depending on whether the machine is working with hay, straw, or silage. This system also increases the density at the bale edges, making them more robust and less susceptible to rain before being transported to the storage site. The bale tying system uses a net, which allows the finished product to be discharged in just six seconds from door opening to closing, resulting in a work cycle always geared towards maximum hourly productivity.
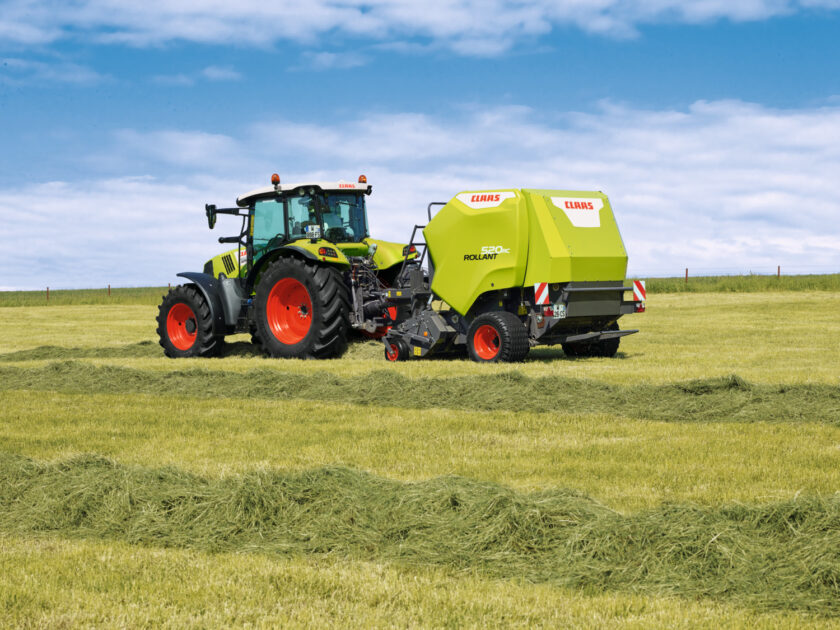
These features are also shared by the fixed chamber “Rollant” balers, which consist of four models with a 210-centimeter-wide pick-up creating a 190-centimeter working front, feeding pressing chambers with diameters of 120 centimeters and widths of 125 centimeters in the “520,” “455,” and “454” models, while the “540” versions offer diameters of 122 centimeters. Rotor options vary by model, with the “Rollant 520” and “Rollant 540” available in both “Roto Feed” and “Roto Cut” configurations, while the “Rollant 455” and “Rollant 454” are only offered in the “Roto Cut” version, which can be integrated with the “Uniwrap” wrapping system. This system wraps six layers of film around the bale in just 23 seconds with a 52 percent overlap using two 750-millimeter arms.
Claas round balers, more Crop with the Same Volume
The harvesting process is optimized by single or double roller compensators, depending on the version, that compress the crop in favor of the subsequent process stages, and the “Maximum Pressure System,” a three-roller group that penetrates up to 20 centimeters into the compression chamber at the start of the process, enhancing product rotation and core compaction. Available also in the “Plus” version, managed through the “Cemis 700” terminal, this system ensures that a bale produced with a greater amount of crop for the same volume, thus optimizing transportation and storage activities.
Protagonist in Harvesting
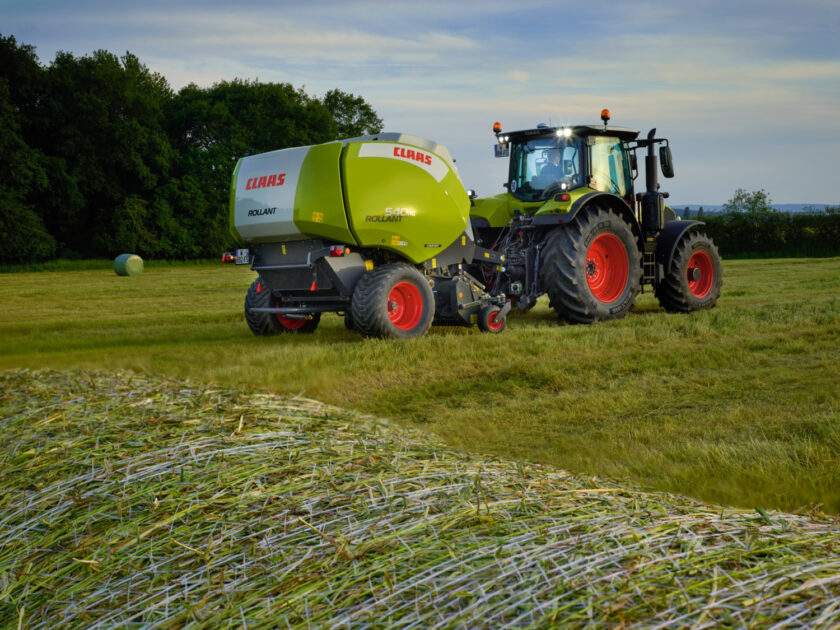
Designed to maximize the productivity of Claas “Variant 500” balers by eliminating the risk of clogging, the “Pro” floor, lowerable by 30 centimeters, operates via two pistons and is managed through the tractor’s onboard terminal. Capable of actively adapting to the crop flow, the system allows movement during work and alerts the user before clogging with a pre-alarm system, enabling a quick operator response. This ensures optimal feeding and safety even in the case of uneven windrows, contributing, along with the “Smart Density” system, to high hourly production in any harvesting condition. This goal is also achieved through Claas engineers’ efforts to minimize downtime due to maintenance needs and to allow the equipment to travel on roads at speeds up to 40 km/h with maximum safety.
Title: Claas “Variant” and “Rollant” round balers: ideal for Uneven Terrain
Translation with ChatGPT